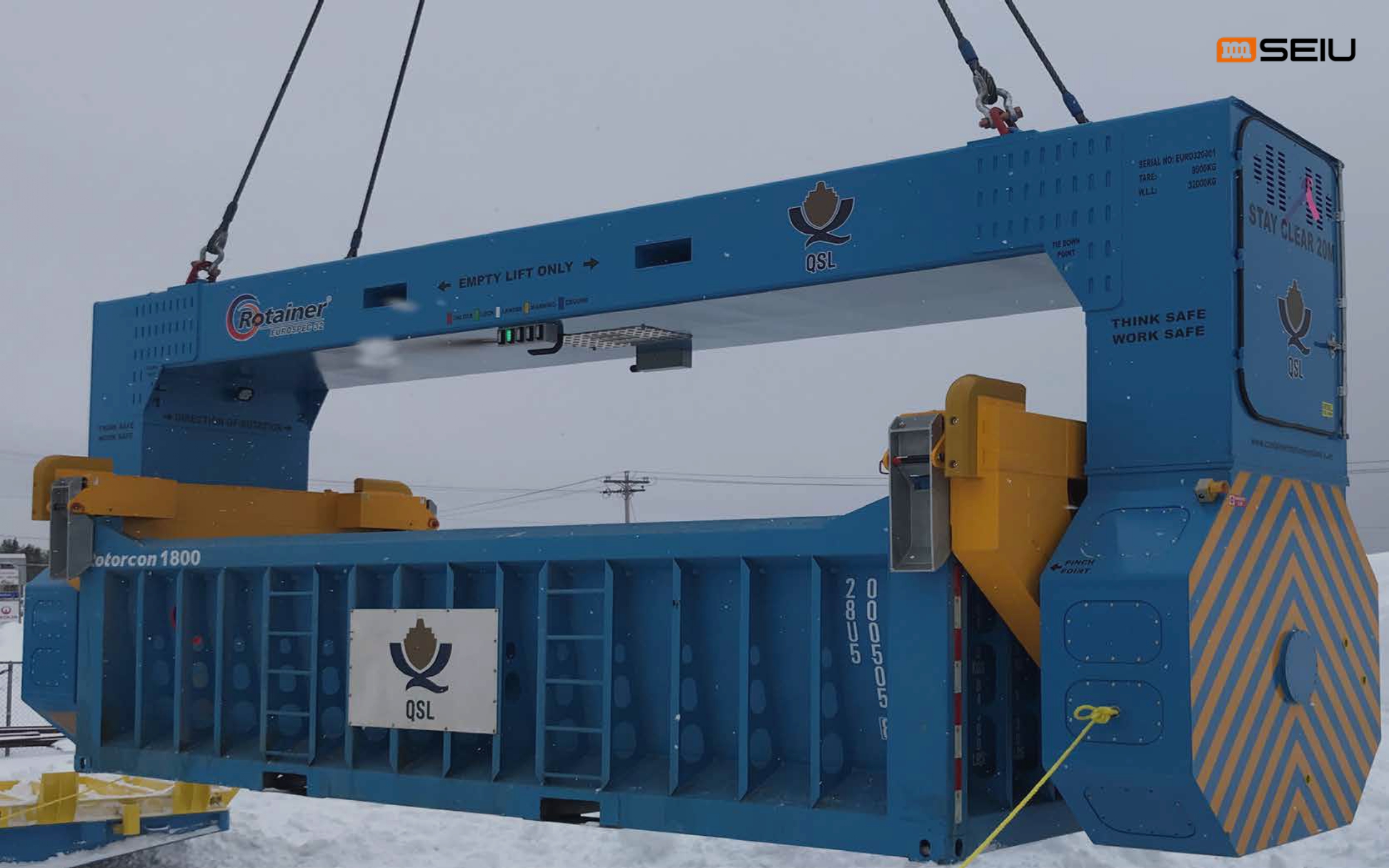
Contents
- Introduction
- In-house handling of bulk cargo in containers
- Transportation of bulk cargo in containers
- Terminal handling of bulk cargo in containers
- Conclusion
Introduction
There are quite a few articles in professional circles about the containerization of bulk handling. Mostly about the advantages of the technology. But almost no figures are given at all! This is understandable. After all, the geography of containerization is quite wide, and each location will have its own calculations. Next, I will show you some figures that you should pay attention to when implementing the technology of containerization of your bulk cargo.
If we break down the logistics chain of containerized cargo into its components, it consists of the following links:
- In-house processing
- Transportation
- Terminal handling
Let’s briefly analyze each link in the format of numbers: productivity, depths, loading rates, carrying capacities, transportation costs, etc. I’ll be quoting data from the part of the world where I live and work.
In-house handling of bulk cargo in containers
At this stage of the logistics chain, containers are loaded, unloaded, and stored for a short time. Some consignees/shippers have their own container terminals and the appropriate lifting equipment. The majority of cargo owners in my part of the world have a fairly good internal infrastructure for handling bulk cargo. This includes their own rail sidings, highways, and indoor or outdoor warehouses. It is clear that each shipper/consignee will have its own calculations of the financial and economic indicators of this link of production costs. To assess the cost of implementing containerization technology, the following will be important:
– Length of railroad sidings. Whether the cargo owner can accept about 54 40-foot or 43 60-foot platforms with 20-foot containers. On a 1435 mm gauge track, this means 20 to 30 60-foot platforms, depending on the country.
– Container loading/unloading rates. The shorter the loading and unloading time, the higher the rolling stock turnover rate. It will be easier to coordinate a container train if the time for loading/unloading containers does not exceed 48 hours. For example, one of our clients has a reefer with Rotainer that handles more than 1200 containers per month.
– Length of the weighing equipment. If you are weighing, for example, railway cars in a static state, it is advisable to have a scale platform at least 18 meters long.
– The area of your internal terminal for storing loaded and empty containers. This figure will depend on the volume of cargo handled. Being able to store a volume that is a multiple of the number of containers you ship per week or, for example, per month will significantly improve your process performance.
Transportation of bulk cargo in containers
This is perhaps the most important and expensive stage of containerization technology. Whether to introduce containerization will largely depend on the cost of transporting containers by one or another mode of transport. In my part of the world, containers with bulk cargo are delivered mainly by rail. And only a small part of them are delivered by road or a combination of rail and road. This is due to dimensional and weight restrictions. On a 1520 mm wide gauge, the cost of a container shipment does not depend on the class and type of bulk cargo. Only the hazard class and the size of the container are affected. The amount of cargo transported in a container will depend on the carrying capacity of the container itself and the railway platform. Our bulk containers have a gross weight of up to 42 tons (specialised containers). The lifting capacity of railway platforms operated on the 1520 gauge track space varies from 60 tons to 80 tons for the new type of platform 13-6851-01. On the 1435 mm track gauge, in addition to the above restrictions, there are also restrictions based on the class of the railroad itself. Here, as a rule, the gross weight of the transported container does not exceed 30 tons. The length of the train is no more than 20-30 60-foot platforms, depending on the country. Below is the cost of shipping a 20-foot container on some routes:
– Hamburg – Mostyska – $1400
– Hamburg – Kyiv – $1800
– Hamburg – Odesa – $1950
– Gdańsk – Mostyska – $1300
– Gdańsk – Kyiv – $1850
– Gdansk – Odesa – $1950
– Copper – Kyiv – $1900
– Koper – Odesa – $1900
– Constanta – Dornesti – $890
– Constanta – Kyiv – $2300
– Constanta – Odesa – $2200
Terminal handling of bulk cargo in containers
It is also an important link in containerization. Its significance in logistics chains increases when the technology is used exclusively for intra-terminal handling of bulk cargo. Containerization is most widely used in port handling. When bulk cargoes are delivered from the rear warehouses of ports in containers to the berth and then unloaded into the vessel’s holds using a Rotainer. Universal container terminals can be used to implement this transshipment scheme. Depending on the size of the port, such a container terminal can have a depth of up to 18 meters at the quay wall. Such a draft can be used by vessels with a carrying capacity of up to 150,000 tons. At large container terminals, loading and unloading operations can be carried out simultaneously by six or more cranes. If the port’s ground services provide the required container handling speed, a skilled crane operator can perform up to 30 cycles per hour. If the net weight of the cargo in the container is, for example, 30 tons, the vessel’s loading rates can reach 120,000 tons per day. This is quite a good performance for such a vessel as the Capesize. The cost of transshipment of containers at a universal container terminal in our region averages about 350 euros per 20-foot container. If the net weight of the cargo in the container is 30 tons, it is about 12 euros per ton.
Rail container terminals can also handle bulk cargo using Rotainer. At such terminals, our spreaders can be installed both on overhead cranes and on reach stackers that handle containers at rail terminals. The speed of loading and unloading operations will, of course, be slower than in a sea or river port, but railroad rolling stock does not transport 150,000 tons of cargo at a time. The maximum carrying capacity of a railroad train consisting of 54 platforms and 108 20-foot containers can reach 3,240 tons with a container load of 30 tons. And on a 1435 mm wide gauge, it is even less – about 1,600 tons maximum. The cost of transshipment of bulk cargo in 20-foot bulk containers at a railway terminal is approximately 60 euros per 20-foot container in case of direct transshipment (according to the wagon-wagon scheme) and approximately 100 euros in case of transshipment according to the wagon-container platform-wagon scheme. In relative terms, when a 30-ton container is loaded, this is about 2 euros and 3.3 euros per ton of cargo, respectively.
Conclusion
Each region has its own specifics of container handling calculations. But most likely, the technology will not differ dramatically. I hope that cargo owners from my part of the world will be able to roughly estimate the cost of handling their bulk cargo using containerization technology based on the data provided.
Author: Mykola Soloviov
You will also be interested in: CBH IS FAST, HIGH-QUALITY AND CHEAP LOGISTICS?